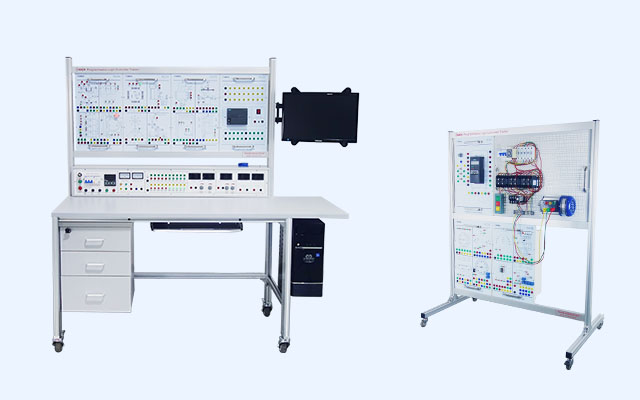
Overview
•The training systems focus on conveying basic knowledge and information on programmable logic control
(PLC) and demonstrate how such systems are networked with sensors and actuators. The fundamentals
and operation of PLC systems are graphically explored using a multitude of examples, explanations,
exercises and practical assignments.
• It covers a huge training range which is widely used in industrial application, including PLC technology,
VFD drive technology, motor control technology, etc.
• Modular experimental panels are adopted for flexible training, coming with standard height that can easily
be inserted into the experiment stands.
TRAINING CONTENT
- PLC mainframe
- Work with STEP 7 programming software
- Programming languages STL, LAD and FBD
- Programming of counters and time makers, comparison and arithmetic functions
- Putting into operation and testing
- Creating statement lists
- Programming of binary operations
- Program structure, invoking subroutings
- Data types
- Demo systems
- Various liquids automatic mixing control
- Automatic vending machine
- Automatic water tower water supply
- Assembly line control
- Automatic goods delivery and loading system
- Plating system
- Music fountain
- Mechanical sliding table (dynamic)
- Mail sorting
- Automatic washing machine
- Spray painting machine control system (dynamic)
- Stepping motor control (dynamic)
- Motor automatic control
- Cutting machine control system (dynamic)
- Manipulator control
- Analog television transmitting tower
- Automatic Elevator control
- Automatic molding machine
- Responder control
- Machining center tool magazine control (dynamic)
- Traffic light control
- Automatic punching machine
- Inverter drive and motor control application
- PID variable frequency speed control (I)
- PLC based UUS control parameter setting
- Stepless speed control
- Multistep speed selection and frequency control
- Frequency converter controlled motor forward and reverse rotation
- PID variable frequency speed control (II)
- Inching control of external terminal
- PLC based MODBUS RTU control object
- Variable speed control under external analog quantity (voltage)
- External button controlled speed-up/speed-down
- Digital quantity based fixed speed control
- Electric drive application (Three-phase asynchronous motor )
- Unidirectional jogging control
- Unidirectional continuous operation with jogging control
- Sequential control
- Y- ? reduction voltage start control program
- Double interlocking forward and rotation control
- Remote and local control
- Unidirectional continuous operation control